Heat pressing machine, including hot forming press, are vital tools in industries like manufacturing, automotive, and composite materials production. These machines offer precise control over high temperatures and pressures, enabling the accurate forming of components for various applications. However, just like any other high-performance equipment, proper maintenance is essential to ensure their longevity, efficiency, and safe operation. This guide will walk you through key practices for maintaining hot pressing machines so you can optimize their performance and reduce downtime.
Table of contents:
Prolonging the Lifespan of Your Hot Forming Press with Proper Maintenance
Identifying Common Issues in Heat Press Machines and Preventing Downtime
Essential Safety Tips for Operating High-Temperature Hot Pressing Machines
The Role of Regular Inspections in Ensuring Heat Press Machine Efficiency
Prolonging the Lifespan of Your Hot Forming Press with Proper Maintenance
Regular maintenance is the backbone of keeping your hot forming press in peak condition. Preventative care not only extends the machine's lifespan but also improves operational reliability. Start with routine cleaning of external and internal machine parts to prevent accumulation of dust and debris that can interfere with the precision of the machine’s components. Make sure the precision machining frame and heating plates are free from residues that could affect accuracy. Lubricate moving parts such as the hydraulic systems and control modules to minimize friction and wear. Regularly inspect and replace worn-out components, including gaskets, seals, and hydraulic filters, which are critical for maintaining performance consistency. Lastly, temperature and pressure calibration are crucial for ensuring the machine operates as intended. Misaligned settings can cause poor product quality and even damage to the machine itself, so using professional-grade calibration tools is a must.
Identifying Common Issues in Heat Press Machines and Preventing Downtime
Identifying potential issues early is essential for reducing downtime and maintaining the efficiency of your heat press machine. Common issues include uneven heating, pressure loss, and alignment problems. Uneven heating can result from dirty or miscalibrated heating plates, so ensure routine cleaning and calibration to maintain uniform temperature distribution. Pressure loss is often caused by hydraulic or pneumatic system leaks—inspect hoses, fittings, and seals regularly to identify signs of wear or degradation. Alignment issues, usually evident from the machine’s inability to produce uniformly shaped components, are another frequent problem. Realignment and recalibration should be performed immediately when misalignment is detected. Additionally, many modern hot pressing machines, such as MEA servo-electric hot forming presses, are equipped with fault monitoring devices. Leverage these diagnostics to identify and address issues before they escalate into major malfunctions.
Essential Safety Tips for Operating High-Temperature Hot Pressing Machines
Operating high-temperature hot pressing machines like the MEA servo-electric hot forming press requires adherence to strict safety protocols to protect operators and equipment. Always ensure the workspace and surrounding area are clear of flammable materials, as the machine can reach temperatures of up to 250°C. Using proper personal protective equipment (PPE), including heat-resistant gloves and safety goggles, is vital for safe handling. Before operating the machine, double-check that all safety guards and covers are securely in place to prevent accidental exposure to moving or heated parts. Operators should also follow standardized procedures for starting and shutting down the machine, particularly when executing processes that involve high-pressure and high-temperature settings. Routine safety drills and equipment inspections can further mitigate risks, ensuring both operator safety and operational efficiency.
The Role of Regular Inspections in Ensuring Heat Press Machine Efficiency
Regular inspections are critical for identifying early signs of wear or functionality issues in hot pressing machines. A detailed inspection schedule should include checking the precision parallelism and flatness of the heating plates, properties crucial for achieving uniform results in your products. For example, the MEA servo-electric hot forming press boasts ±0.02mm precision in parallelism and flatness—any deviation from these values can significantly reduce production quality. Inspection should also cover controls such as the PLC control system and digital display, as software glitches or hardware malfunctions can disrupt operation. Furthermore, regularly monitoring the machine’s heating system is vital for performance. Section-compartmentalized heating systems, such as those found in high-end models, should maintain temperature control uniformity with an accuracy rate of ±0.02%. Addressing discrepancies promptly ensures consistent results and prevents unnecessary downtime.
In conclusion, taking time to appreciate the beauty of nature and engage with the world around us offers countless rewards. It not only nourishes our physical health but also rejuvenates our minds and spirits. By finding moments to connect with our environment, we can cultivate a deeper sense of fulfillment and well-being in our lives.
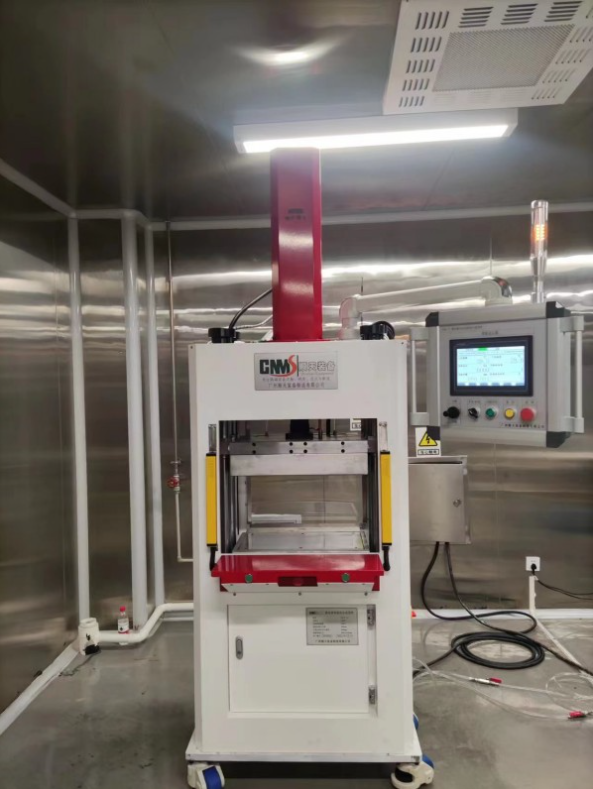
No comments:
Post a Comment